Protect Your Supply Chain
We analyse and certify parts within your inventory that are at most risk of causing your business harm if unavailable.
This guarantees delivery of your parts if for any reason they can not be sourced or there are delays that could affect your business and customer satisfaction.
This guarantees delivery of your parts if for any reason they can not be sourced or there are delays that could affect your business and customer satisfaction.
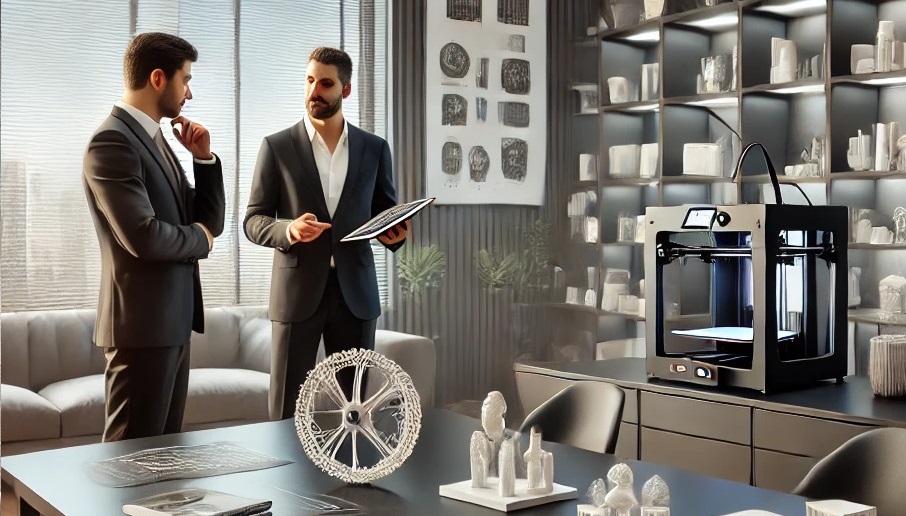
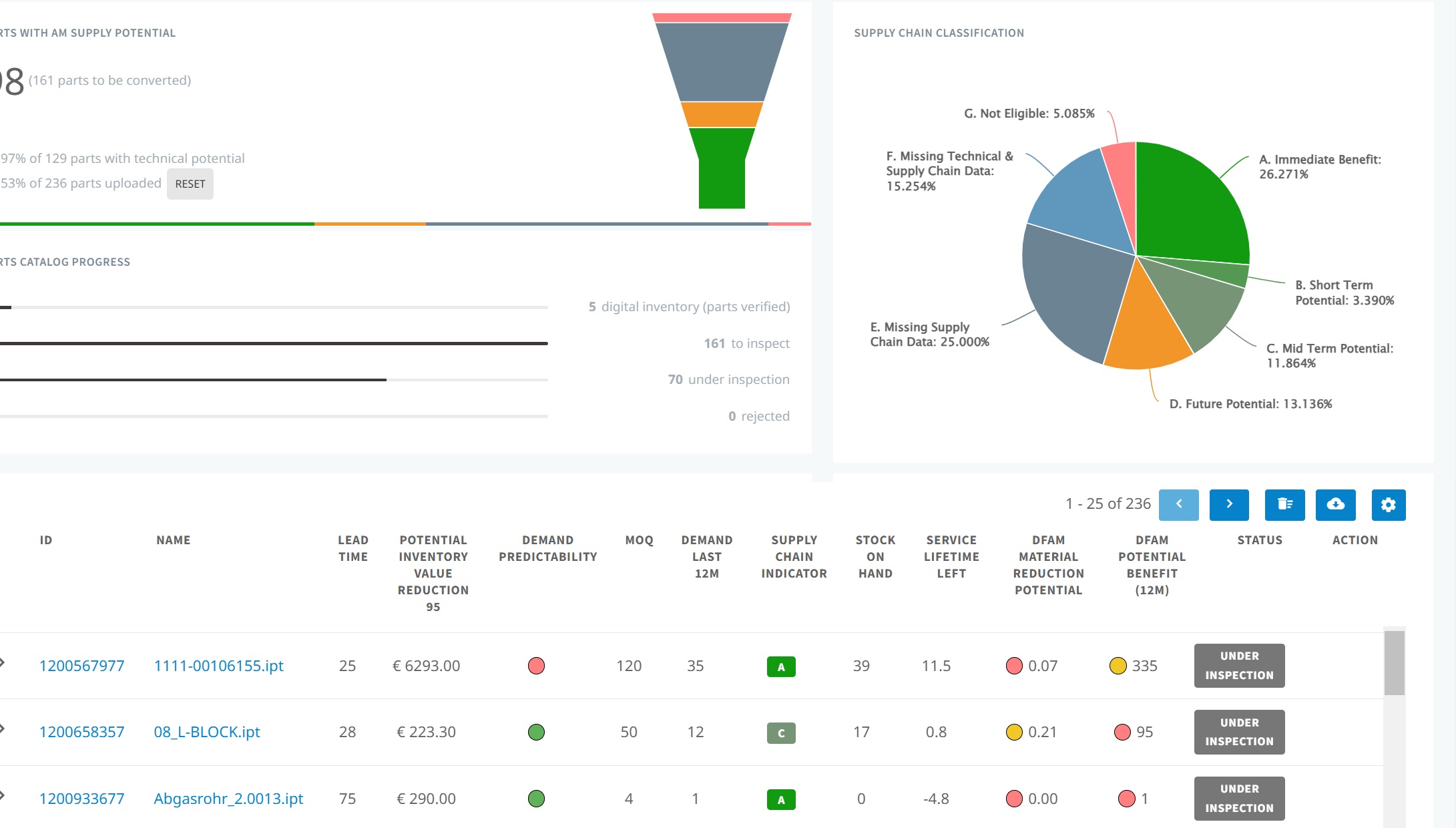
Expert Insights to Plan Your Next Move
Our platform and analytics identifies opportunities to save money through re-design and where applying AM reduces carbon emissions in your manufacturing and supply chain to contribute to a greener world. We also offer services and expertise to support your business as necessary to ensure your supply chain is future proof should the worst happen!
Maximum Performance
We understand your needs in order to quickly deliver parts that meet the quality certification you need for your business, producing and delivering these where needed across the globe.
Should your business lack 3D CAD or data for analysis, our 3D scanning and data extraction services ensure you are not stifled by data deficit in your Additive Manufacturing adoption.
Should your business lack 3D CAD or data for analysis, our 3D scanning and data extraction services ensure you are not stifled by data deficit in your Additive Manufacturing adoption.
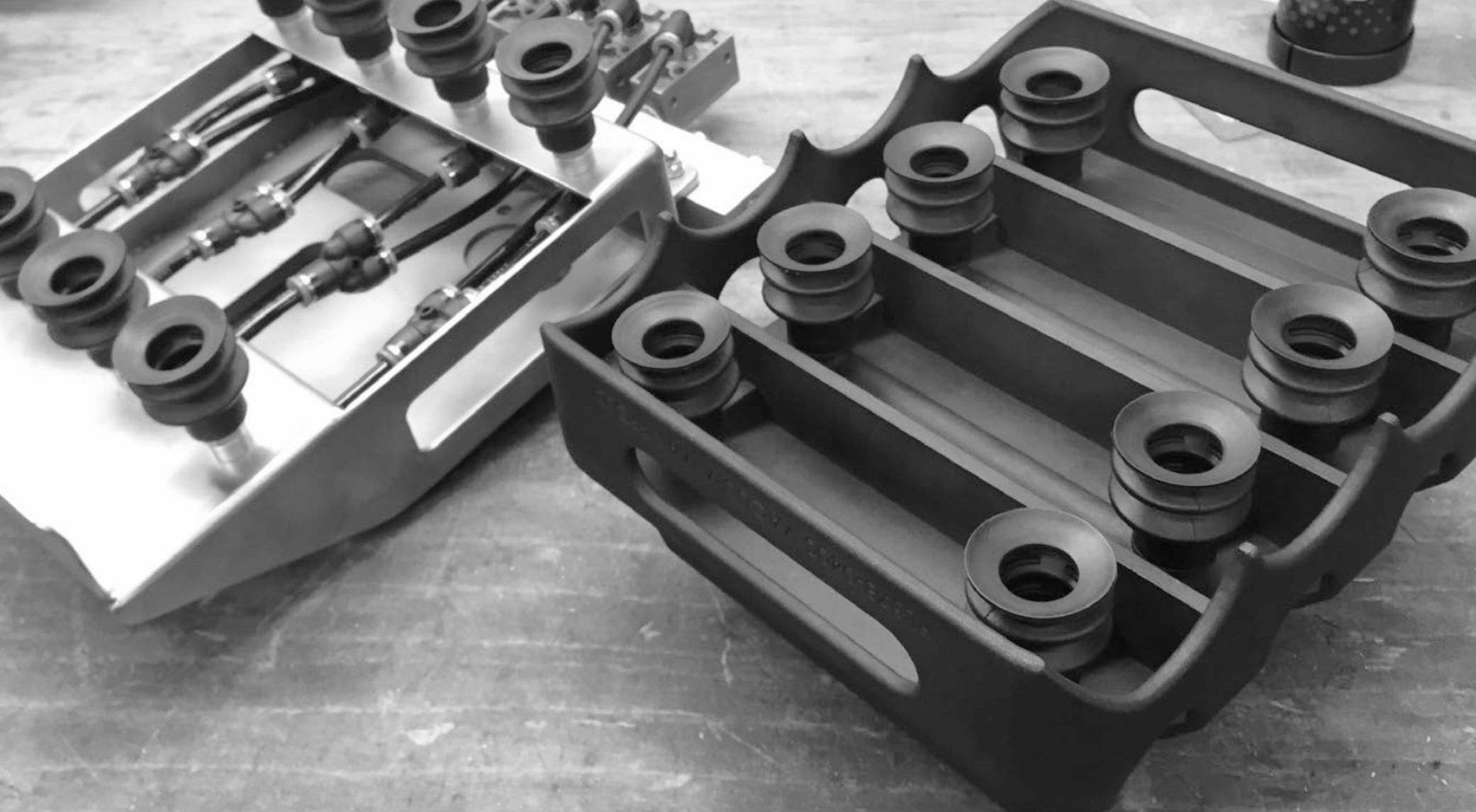
Testimonials that Speak Volumes
Pricing
Flexible Pricing Plans to Suit Your Needs
Choose from our range of affordable pricing options. No hidden fees, transparent and straightforward.
$ 0.00 USD
/ Year
Perfect for smaller businesses to see how and where Additive Manufacturing can adopted
Analyse up to 2000x lines of data
Printability, business, ESG and design analytics
Quote and order in over 40x Materials
Digitisation and redesign services
Expert consultancy available on request
Save 20%
Free
$ 0.00 USD
/ Year
Perfect for smaller businesses to see how and where Additive Manufacturing can adopted
Analyse up to 2000x lines of data
Printability, business, ESG and design analytics
Quote and order in over 40x Materials
Digitisation and redesign services
Expert consultancy available on request
Save 20%
$ 15.00 USD
/ Year
Fully supported service to assist adoption and scaling of Additive Manufacturing within lage businesses
Unlimited analysis of parts
Detailed actionable business insights
Expert consultants to support your AM adoption
Quote and order from 3000x+ materials
Reduce carbon footprint by producing locally
Global sourcing of local supply
Save 20%
Free
$ 15.00 USD
/ Year
Fully supported service to assist adoption and scaling of Additive Manufacturing within lage businesses
Unlimited analysis of parts
Detailed actionable business insights
Expert consultants to support your AM adoption
Quote and order from 3000x+ materials
Reduce carbon footprint by producing locally
Global sourcing of local supply
Save 20%
$ 20.00 USD
/ Year
For agencies with unlimited projects
API Integration available
Give your customers more value from their data
Analytics to optimise supply chains using AM
Help users identify CO2 reduction opportunities
Show where parts can be redesigned for AM
Help customers move to zero inventory
Reduce lead-times
Integrate Dimanex end-end global marketplace
Help to source 'emergency' parts
Save 20%
Free
$ 20.00 USD
/ Year
For agencies with unlimited projects
API Integration available
Give your customers more value from their data
Analytics to optimise supply chains using AM
Help users identify CO2 reduction opportunities
Show where parts can be redesigned for AM
Help customers move to zero inventory
Reduce lead-times
Integrate Dimanex end-end global marketplace
Integrate Dimanex end-end global marketplace
Save 20%
$ 0.00 USD
/ Month
Perfect for smaller businesses to see how and where Additive Manufacturing can adopted
Analyse up to 2000x lines of data
Printability, business, ESG and design analytics
Quote and order in over 40x Materials
Digitisation and redesign services
Expert consultancy available on request
Free
$ 0.00 USD
/ Month
Perfect for smaller businesses to see how and where Additive Manufacturing can adopted
Analyse up to 2000x lines of data
Printability, business, ESG and design analytics
Quote and order in over 40x Materials
Digitisation and redesign services
Expert consultancy available on request
$ 15.00 USD
/ Month
Fully supported service to assist adoption and scaling of Additive Manufacturing within lage businesses
Unlimited analysis of parts
Detailed actionable business insights
Expert consultants to support your AM adoption
Quote and order from 3000x+ materials
Reduce carbon footprint by producing locally
Global sourcing of local supply
Free
$ 15.00 USD
/ Month
Fully supported service to assist adoption and scaling of Additive Manufacturing within lage businesses
Unlimited analysis of parts
Detailed actionable business insights
Expert consultants to support your AM adoption
Quote and order from 3000x+ materials
Reduce carbon footprint by producing locally
Global sourcing of local supply
$ 20.00 USD
/ Month
For agencies with unlimited projects
API Integration available
Give your customers more value from their data
Analytics to optimise supply chains using AM
Help users identify CO2 reduction opportunities
Show where parts can be redesigned for AM
Help customers move to zero inventory
Reduce lead-times
Integrate Dimanex end-end global marketplace
Help to source 'emergency' parts
Free
$ 20.00 USD
/ Month
For agencies with unlimited projects
API Integration available
Give your customers more value from their data
Analytics to optimise supply chains using AM
Help users identify CO2 reduction opportunities
Show where parts can be redesigned for AM
Help customers move to zero inventory
Reduce lead-times
Integrate Dimanex end-end global marketplace
Integrate Dimanex end-end global marketplace
Trusted by
The Dimanex Difference
Powerful Tools,
Limitless Possibilities
Our end to end solution has all the features you need to embrace Additive Manufacturing within your orgnisation
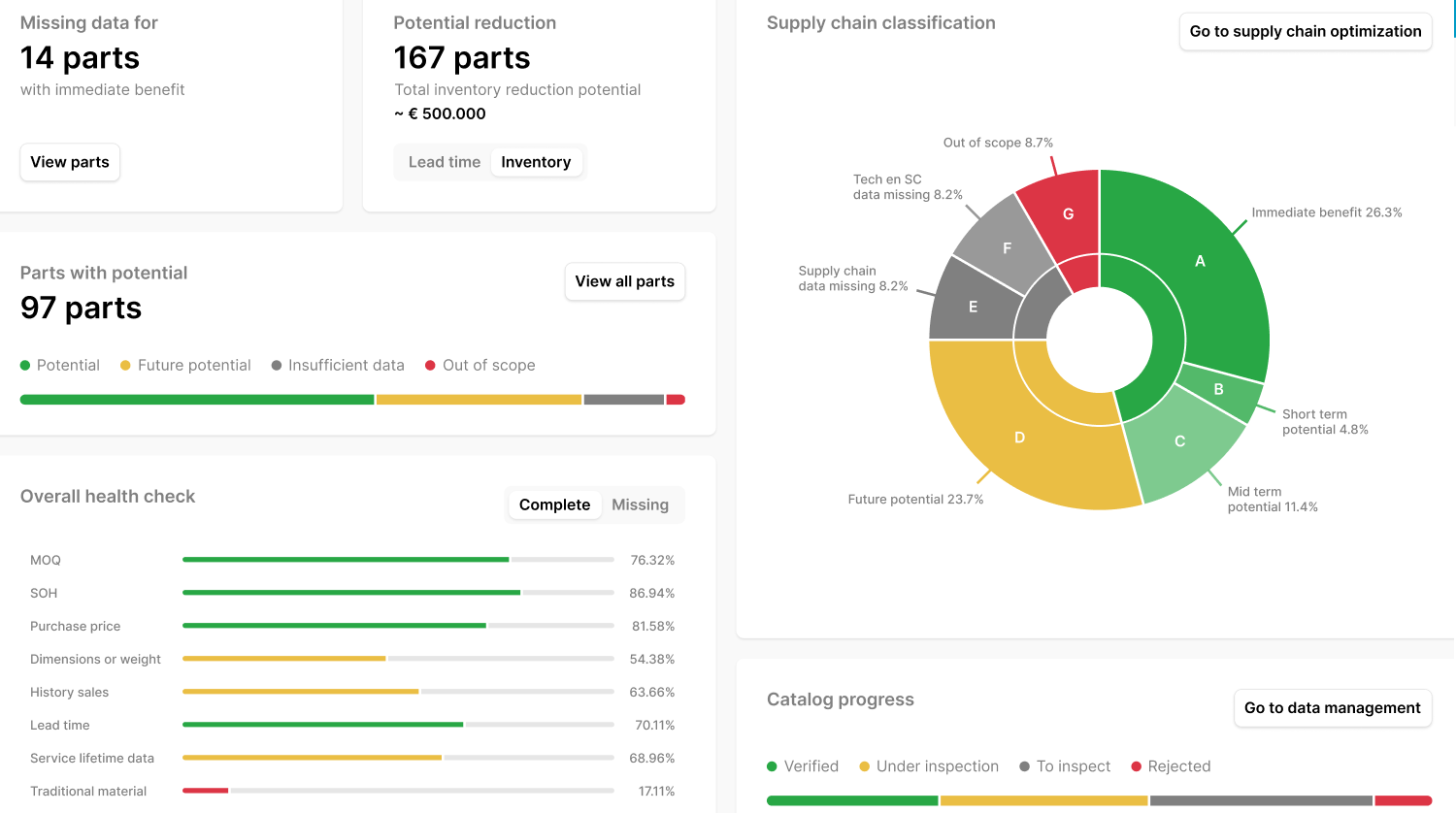
One-Stop-Shop
Perform inventory analysis, upload parts, order and manage all on one cloud-based platform
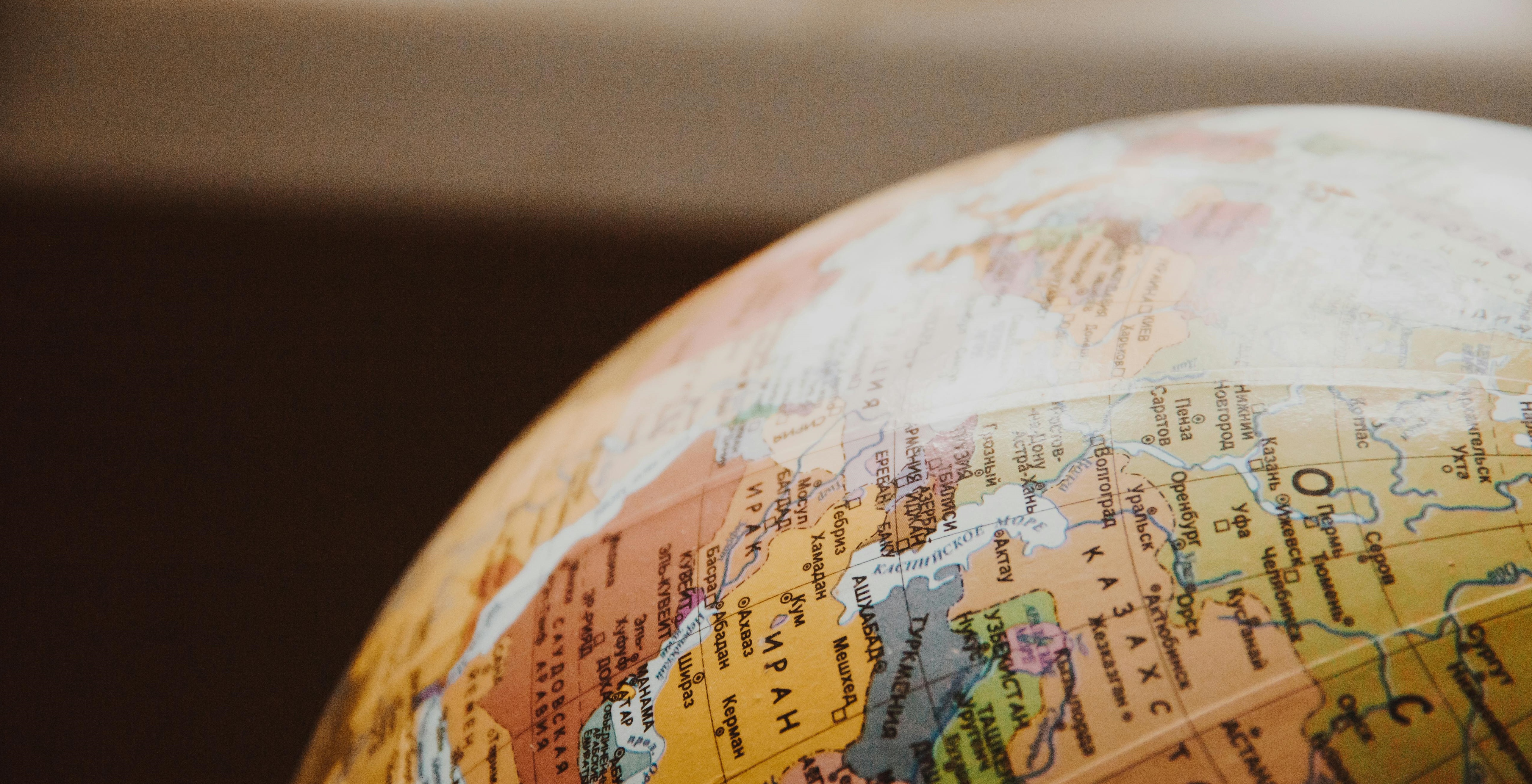
Global Supply Chain
Reduce reliance on remote suppliers with a digital inventory to order parts locally to where they are needed.
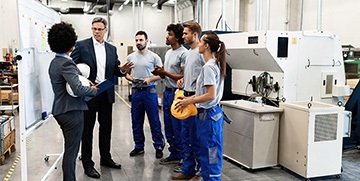
Training and Skills
At Dimanex, we can offer and run training courses in AM and DFAM to suit your business needs
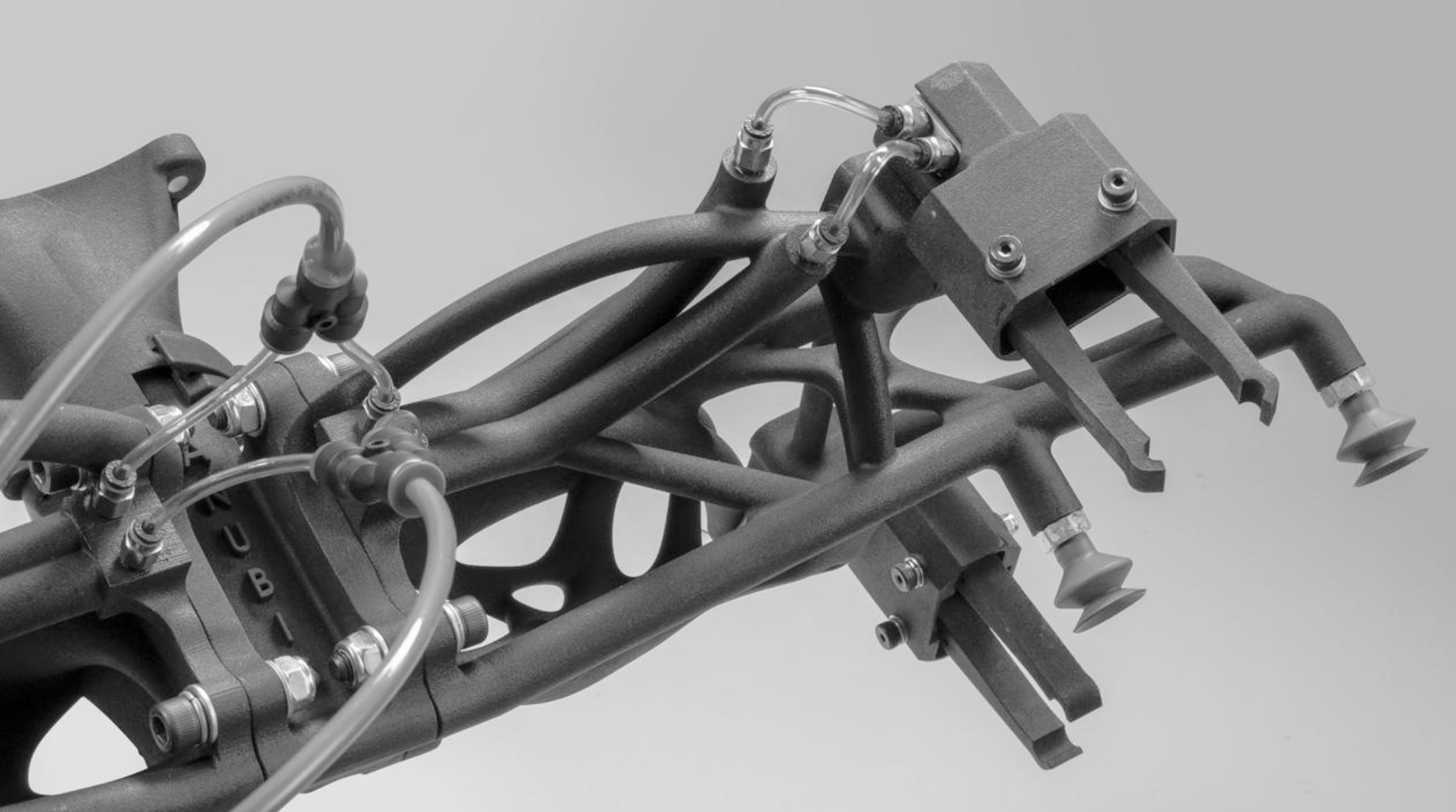
Design for AM
Use our analytics to find which parts would benefit from redesign, then use our services to make it happen!

Consultancy
Lean on our expertise to accelerate your adoption of AM an make the most of benefits even sooner!
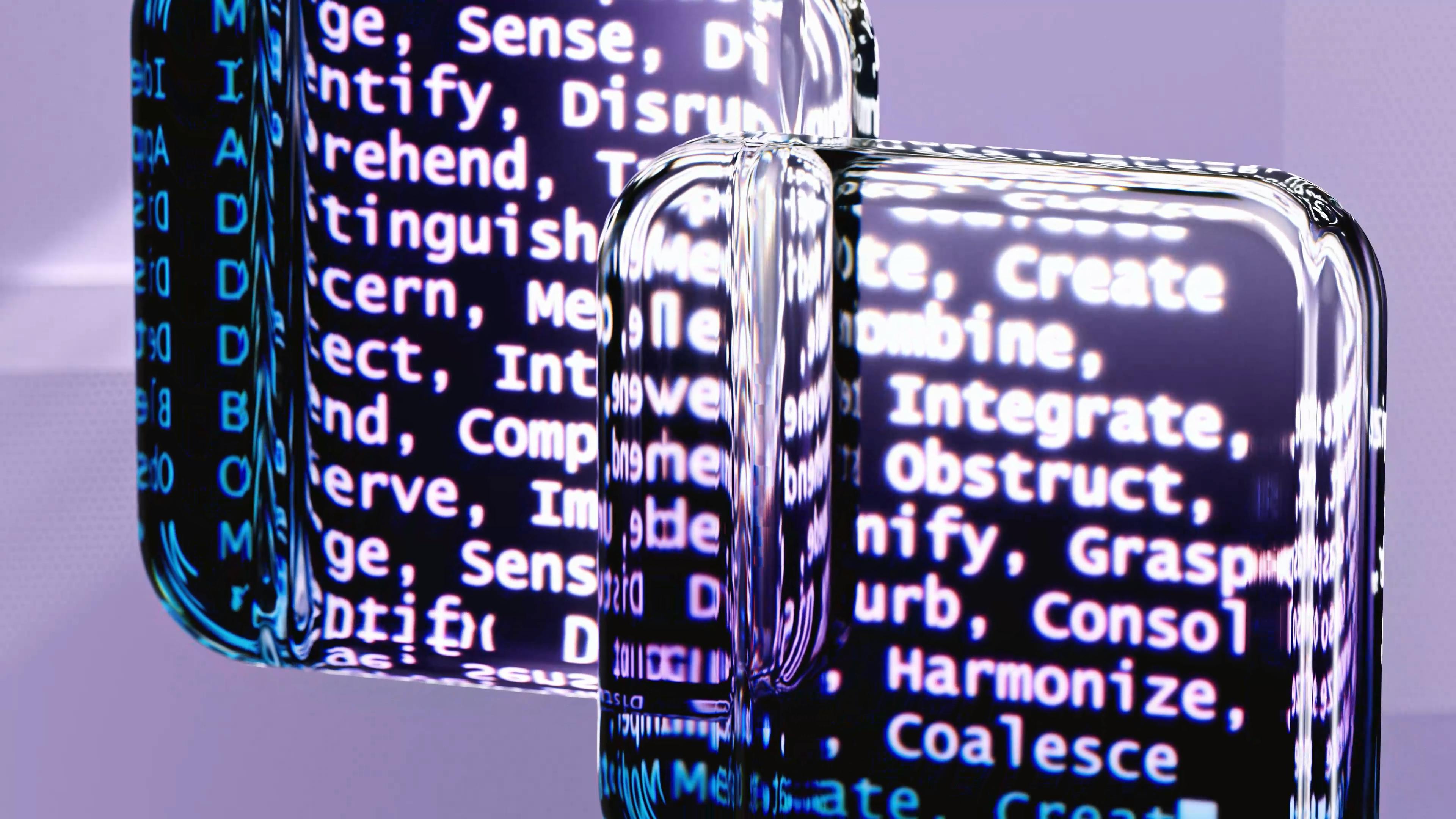
Partner Integrations
Seamless integrations with your existing engineering resource planning design software and procurement systems
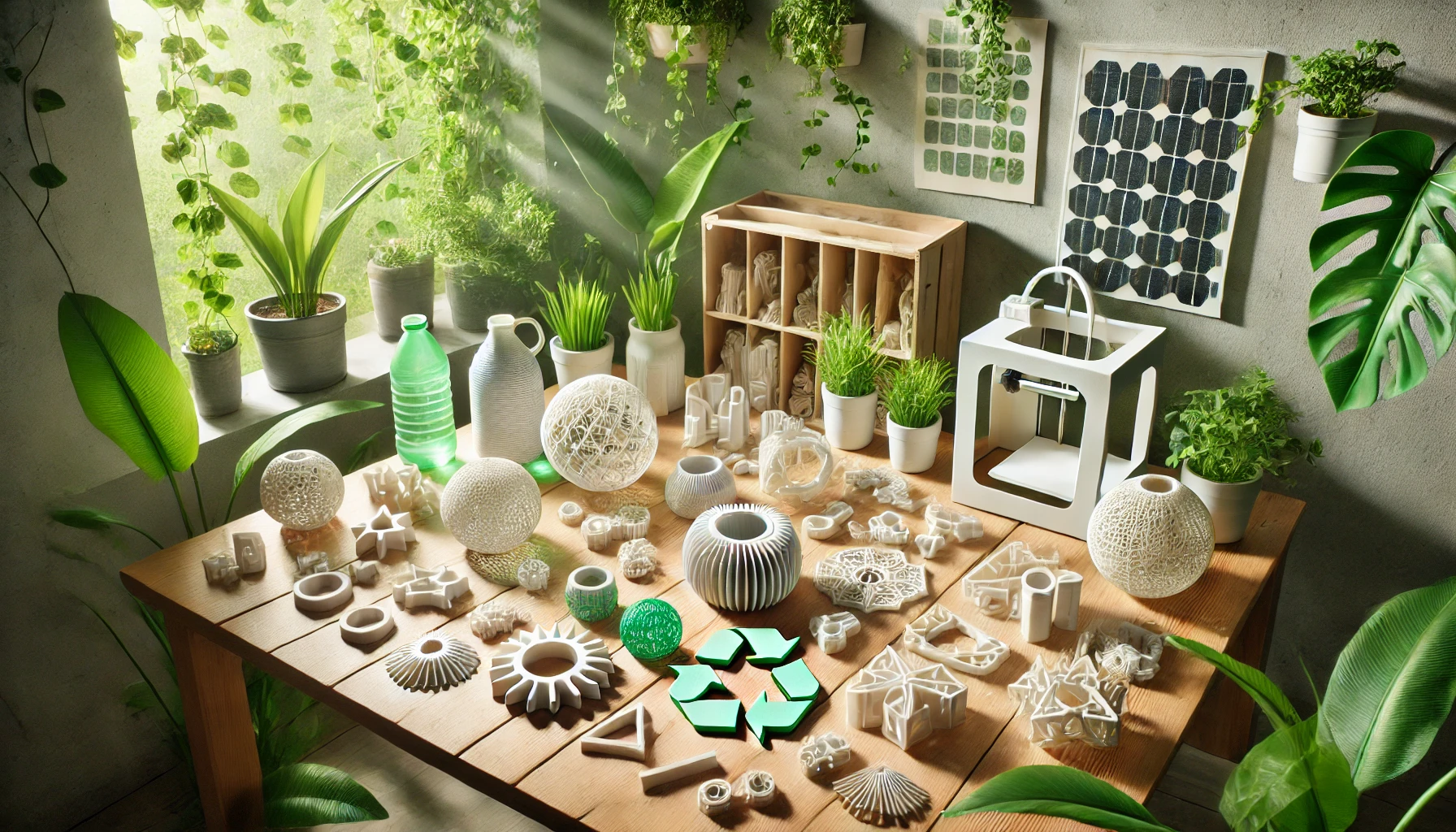
Sustainability
Additive Manufacturing reduces carbon emissions and waste in your supply chains. We identify where you can make gains
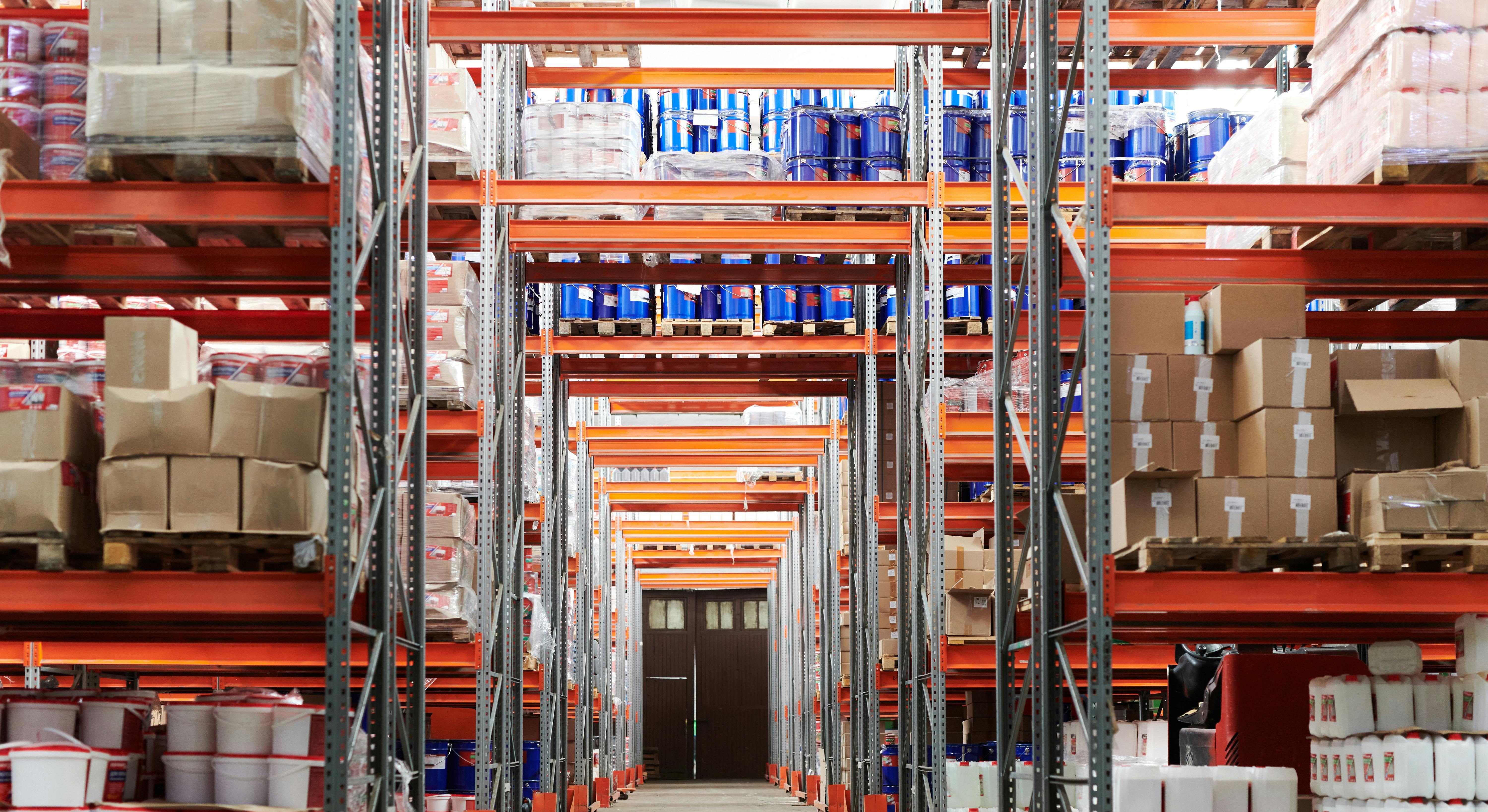
Zero Inventory
Unlock trapped working capital through stockreduction using Additive Manufacturing and eliminate Minimum Order Quantitites