Achieve Your Sustainability Goals
Henk Jonker COO & co-founder: “At DiManEx we like to see that all we do contributes to a much more sustainable world. DiManEx enables company’s transitions from traditional supply chains based on the movement of physical goods, to a digital and sustainable supply chain.”
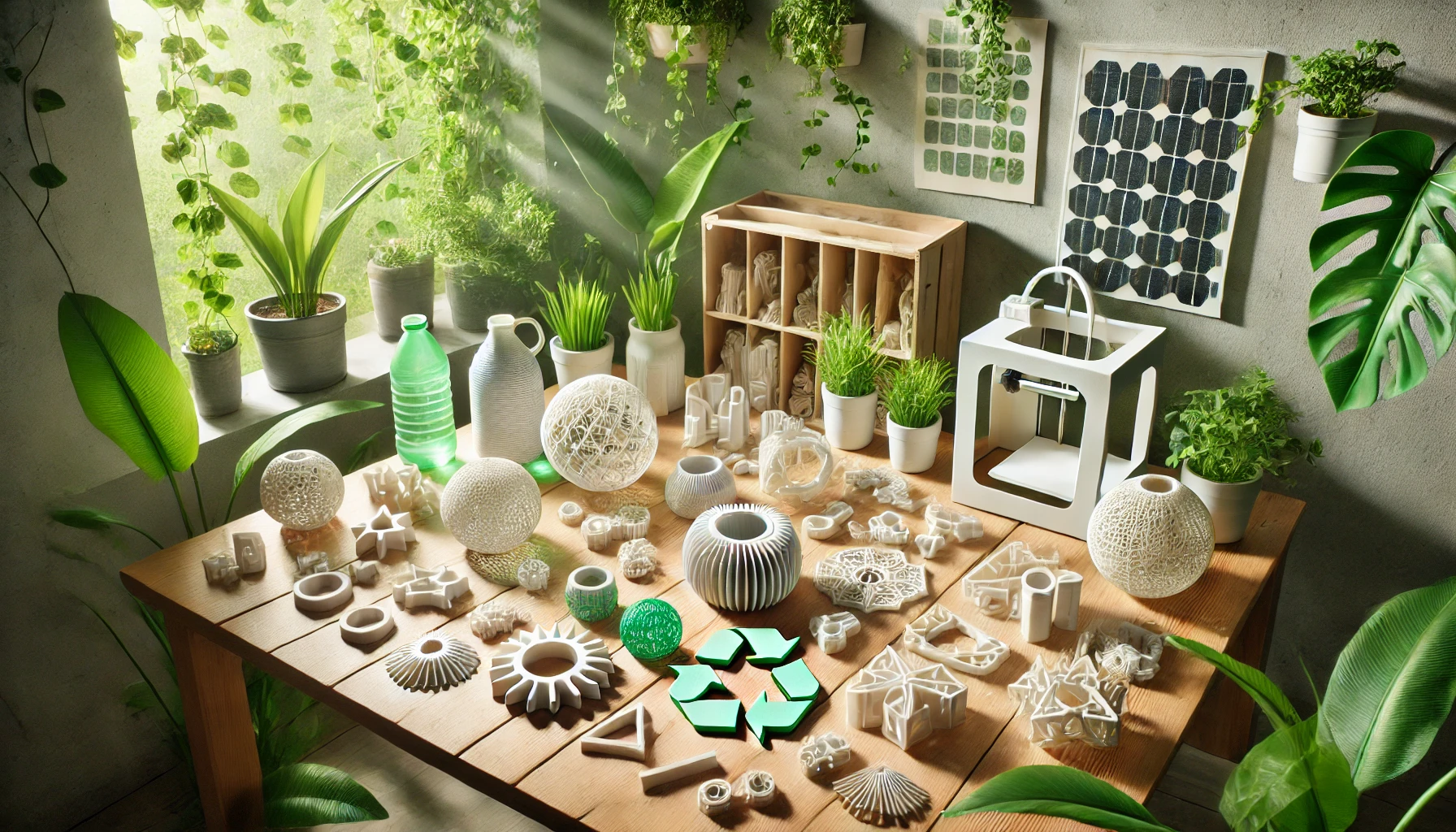
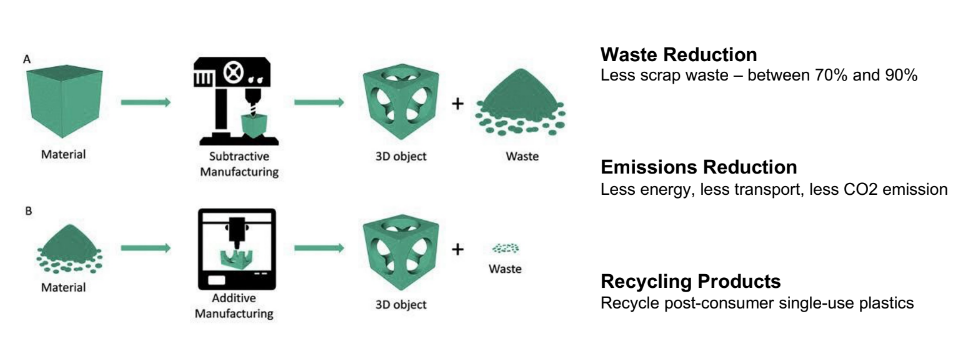
Less Waste, More Value
Additive manufacturing applied in supply chains can reduce waste and CO2 emission significantly. Producing (printing) parts locally and on demand will reduce the amount of parts produced and will reduce the global transport miles.
R-Ladder of Circularity
The PBL Netherlands Environmental Assessment Agency set up a circularity ladder, the so-called R-ladder, in which various strategies are described that contribute to a reduced use of new resources. This R-ladder can be used to ‘measure’ the circularity of supply chains, production, and parts handling.
DiManEx offers products and services that to a certain extend contribute to all levels in the R-ladder, with emphasis on the highest levels.
DiManEx offers products and services that to a certain extend contribute to all levels in the R-ladder, with emphasis on the highest levels.
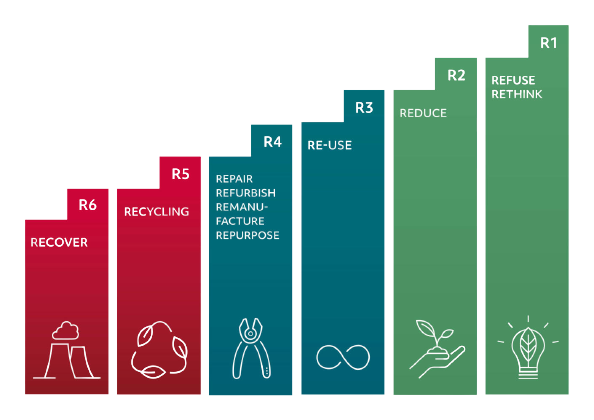
Testimonials that Speak Volumes
Pricing
Flexible Pricing Plans to Suit Your Needs
Choose from our range of affordable pricing options. No hidden fees, transparent and straightforward.
$ 0.00 USD
/ Year
Perfect for smaller businesses to see how and where Additive Manufacturing can adopted
Analyse up to 2000x lines of data
Printability, business, ESG and design analytics
Quote and order in over 40x Materials
Digitisation and redesign services
Expert consultancy available on request
Save 20%
Free
$ 0.00 USD
/ Year
Perfect for smaller businesses to see how and where Additive Manufacturing can adopted
Analyse up to 2000x lines of data
Printability, business, ESG and design analytics
Quote and order in over 40x Materials
Digitisation and redesign services
Expert consultancy available on request
Save 20%
$ 15.00 USD
/ Year
Fully supported service to assist adoption and scaling of Additive Manufacturing within lage businesses
Unlimited analysis of parts
Detailed actionable business insights
Expert consultants to support your AM adoption
Quote and order from 3000x+ materials
Reduce carbon footprint by producing locally
Global sourcing of local supply
Save 20%
Free
$ 15.00 USD
/ Year
Fully supported service to assist adoption and scaling of Additive Manufacturing within lage businesses
Unlimited analysis of parts
Detailed actionable business insights
Expert consultants to support your AM adoption
Quote and order from 3000x+ materials
Reduce carbon footprint by producing locally
Global sourcing of local supply
Save 20%
$ 20.00 USD
/ Year
For agencies with unlimited projects
API Integration available
Give your customers more value from their data
Analytics to optimise supply chains using AM
Help users identify CO2 reduction opportunities
Show where parts can be redesigned for AM
Help customers move to zero inventory
Reduce lead-times
Integrate Dimanex end-end global marketplace
Help to source 'emergency' parts
Save 20%
Free
$ 20.00 USD
/ Year
For agencies with unlimited projects
API Integration available
Give your customers more value from their data
Analytics to optimise supply chains using AM
Help users identify CO2 reduction opportunities
Show where parts can be redesigned for AM
Help customers move to zero inventory
Reduce lead-times
Integrate Dimanex end-end global marketplace
Integrate Dimanex end-end global marketplace
Save 20%
$ 0.00 USD
/ Month
Perfect for smaller businesses to see how and where Additive Manufacturing can adopted
Analyse up to 2000x lines of data
Printability, business, ESG and design analytics
Quote and order in over 40x Materials
Digitisation and redesign services
Expert consultancy available on request
Free
$ 0.00 USD
/ Month
Perfect for smaller businesses to see how and where Additive Manufacturing can adopted
Analyse up to 2000x lines of data
Printability, business, ESG and design analytics
Quote and order in over 40x Materials
Digitisation and redesign services
Expert consultancy available on request
$ 15.00 USD
/ Month
Fully supported service to assist adoption and scaling of Additive Manufacturing within lage businesses
Unlimited analysis of parts
Detailed actionable business insights
Expert consultants to support your AM adoption
Quote and order from 3000x+ materials
Reduce carbon footprint by producing locally
Global sourcing of local supply
Free
$ 15.00 USD
/ Month
Fully supported service to assist adoption and scaling of Additive Manufacturing within lage businesses
Unlimited analysis of parts
Detailed actionable business insights
Expert consultants to support your AM adoption
Quote and order from 3000x+ materials
Reduce carbon footprint by producing locally
Global sourcing of local supply
$ 20.00 USD
/ Month
For agencies with unlimited projects
API Integration available
Give your customers more value from their data
Analytics to optimise supply chains using AM
Help users identify CO2 reduction opportunities
Show where parts can be redesigned for AM
Help customers move to zero inventory
Reduce lead-times
Integrate Dimanex end-end global marketplace
Help to source 'emergency' parts
Free
$ 20.00 USD
/ Month
For agencies with unlimited projects
API Integration available
Give your customers more value from their data
Analytics to optimise supply chains using AM
Help users identify CO2 reduction opportunities
Show where parts can be redesigned for AM
Help customers move to zero inventory
Reduce lead-times
Integrate Dimanex end-end global marketplace
Integrate Dimanex end-end global marketplace
Trusted by
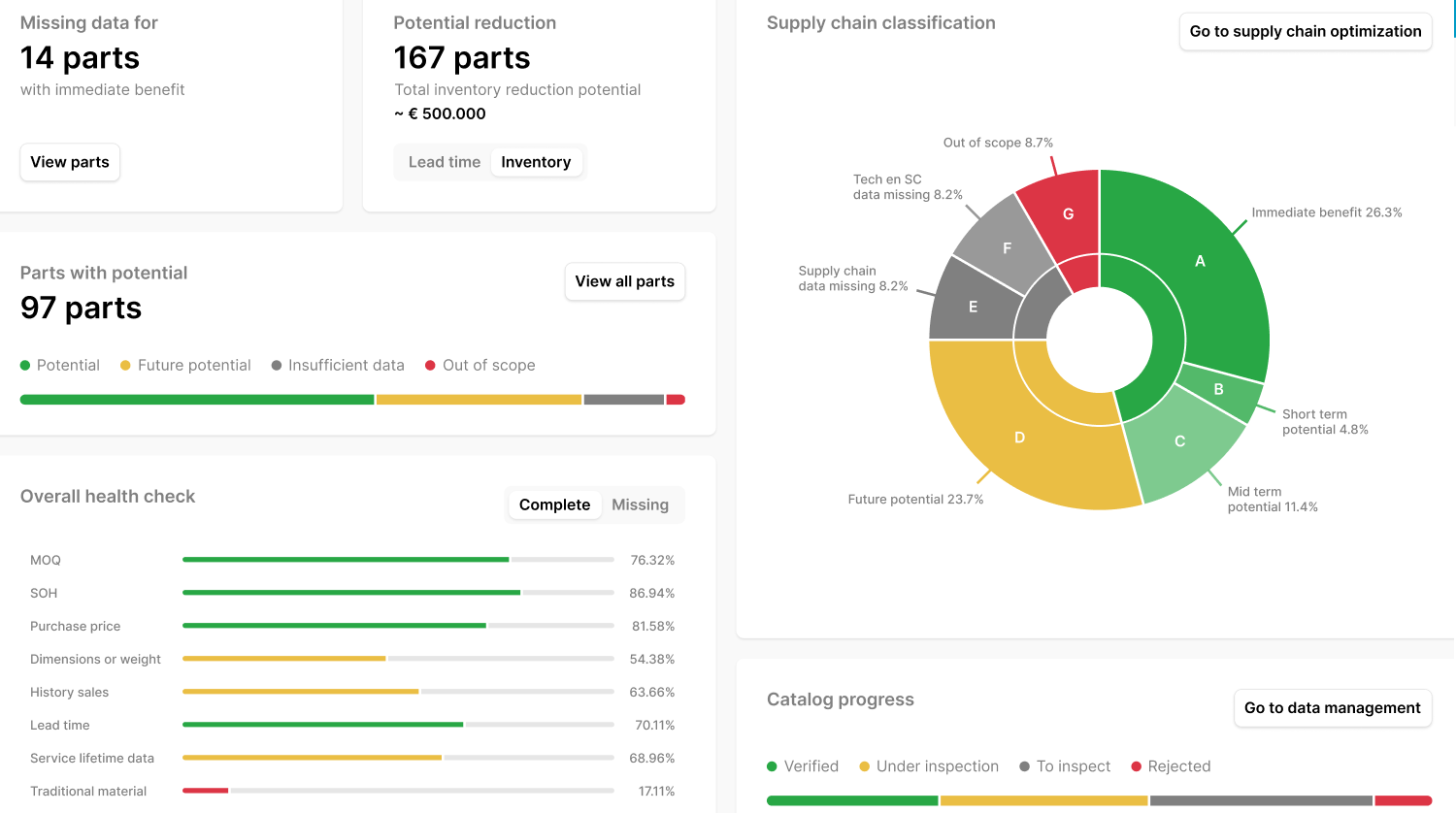
One Stop Shop
Perform inventory analysis, upload parts, order and manage all on one cloud based platform
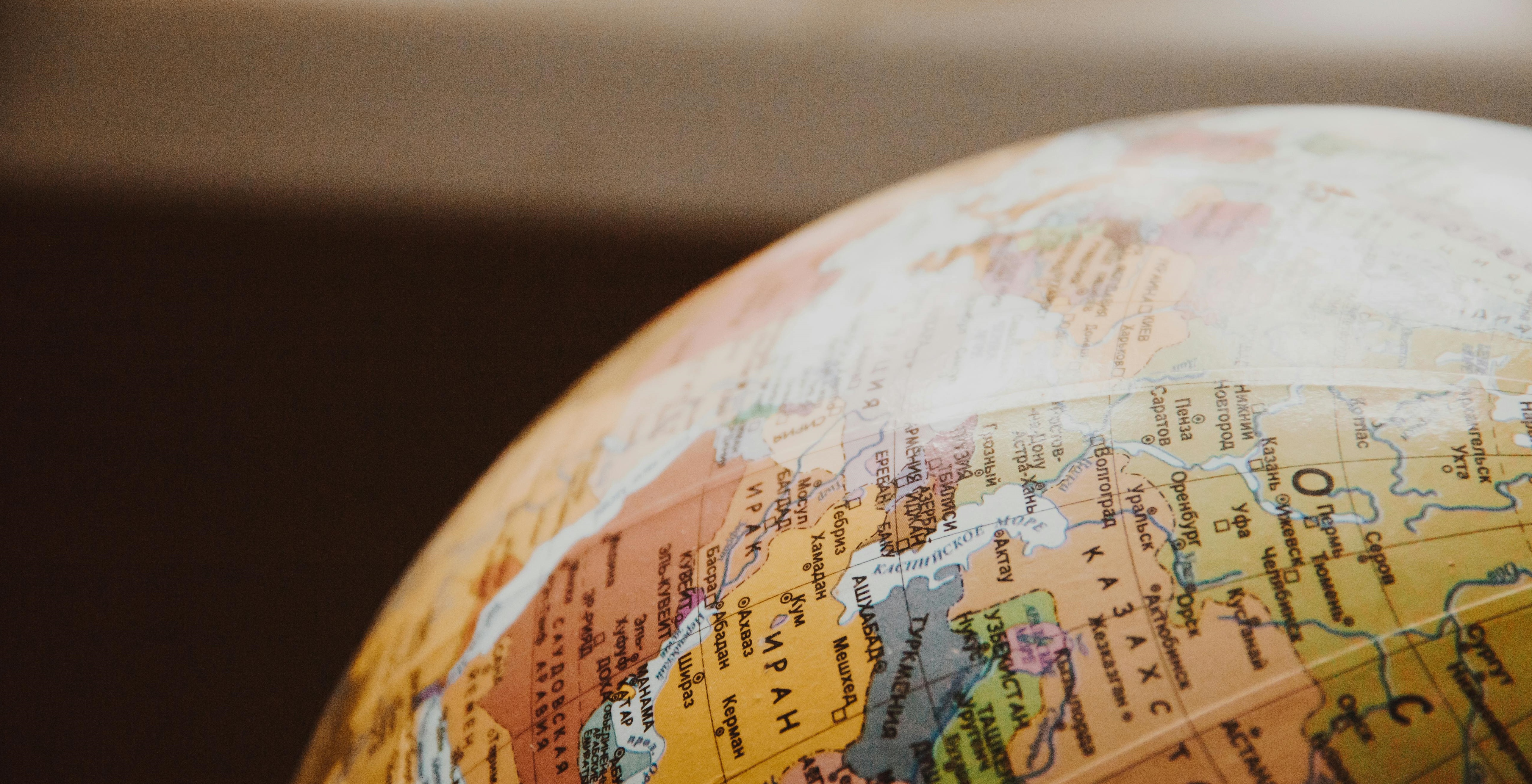
Global Supply Chain
Reduce reliance on remote suppliers with a digital inventory to order parts locally to where they are needed.
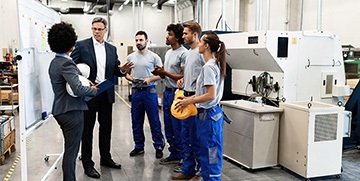
Training and Skills
At Dimanex we can offer and run training courses in AM and DFAM to suit your business needs
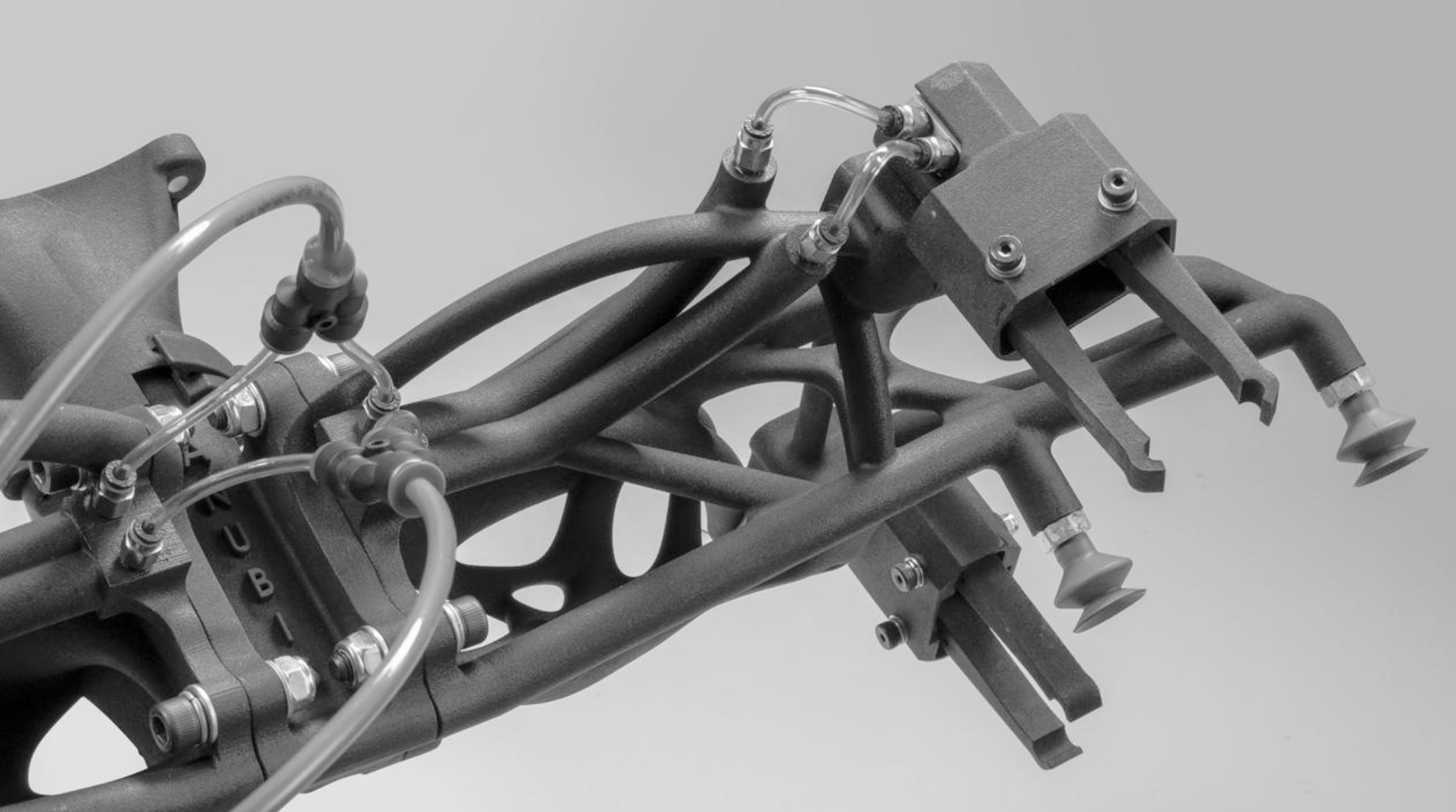
Design for AM
Use our analytics to find which parts would benefit from redesign, then use our services to make it happen!

Consultancy
Lean on our expertise to expedite your adoption of AM an make the most of benefits even sooner!
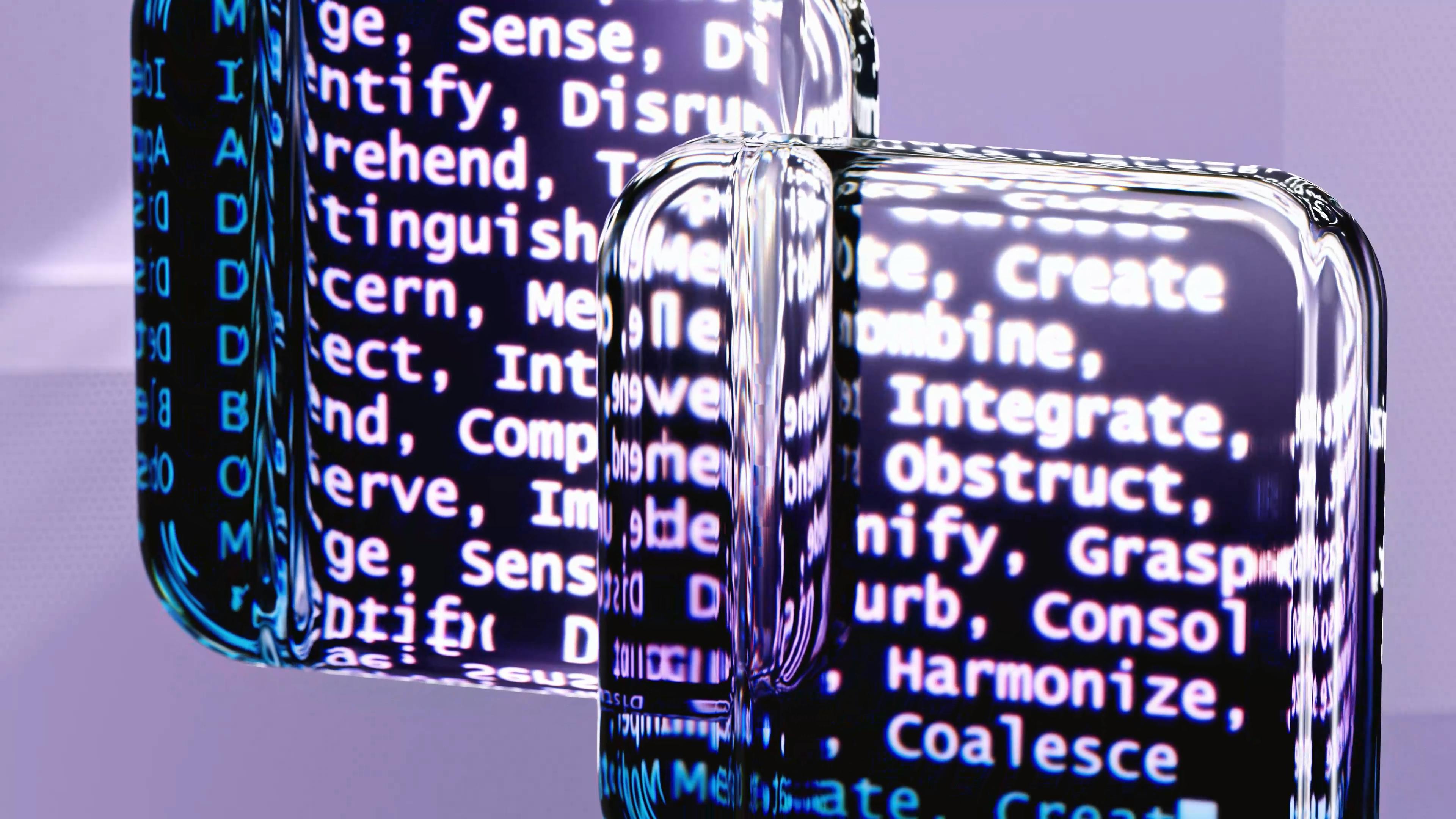
Partner Integrations
Seamless integrations with your existing engineering resource planning and design software
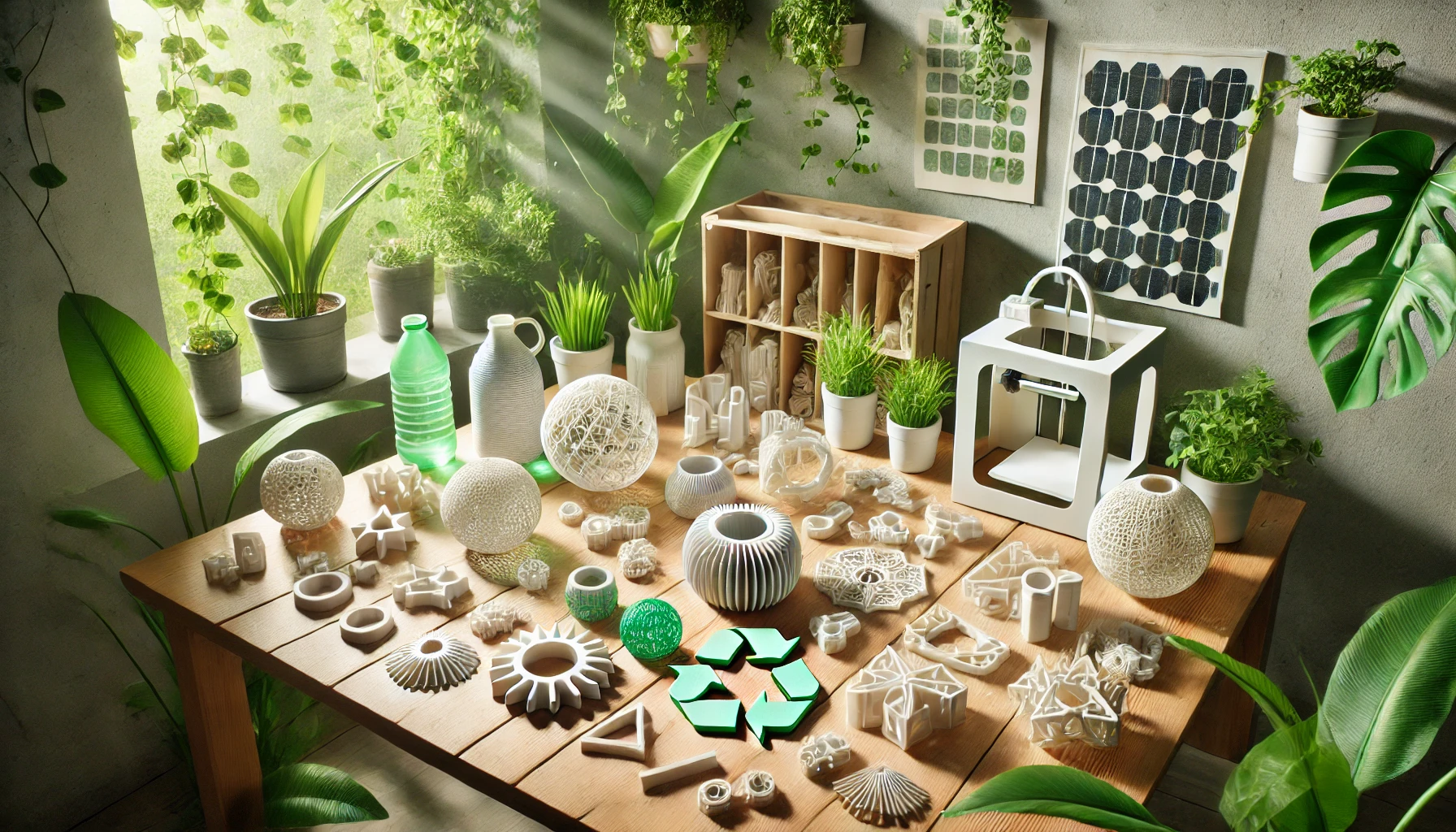
Sustainability
Additive Manufacturing reduces waste which is great for the environment! Let us identify where you can make gains!
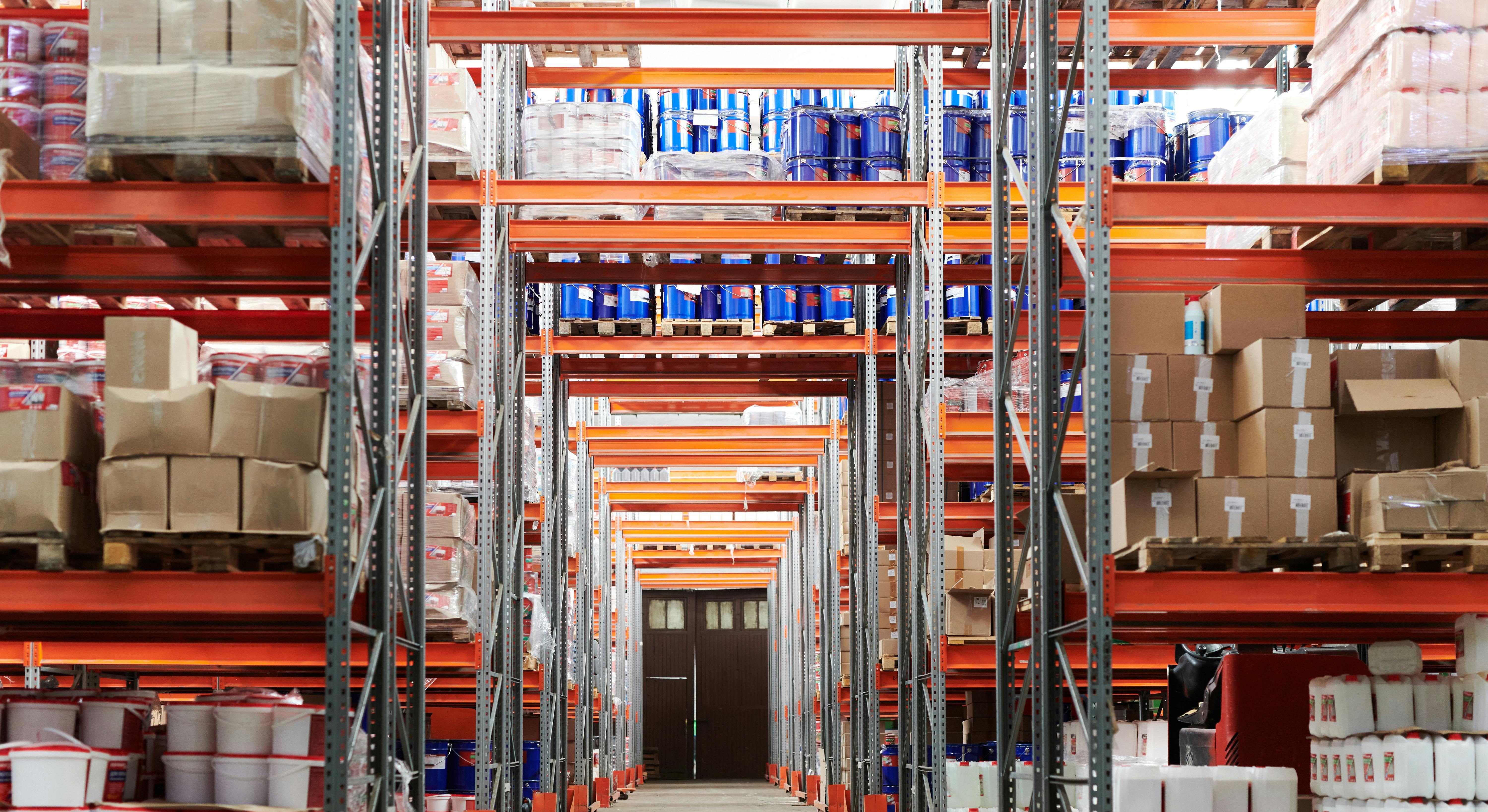
Zero Inventory
Unlock trapped capital through stock reduction using Additive Manufacturing which has no minimum order quantities